Varnish Removal: Answers to Frequently Asked Questions
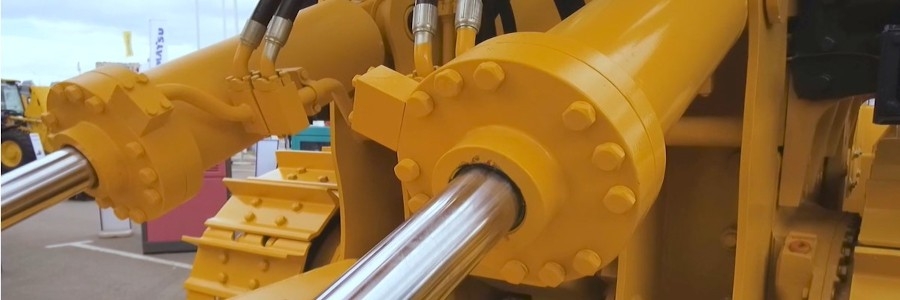
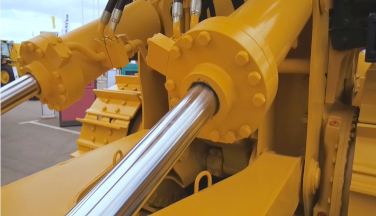
Varnish is a common problem in all types of lubricated equipment – turbines, compressors, hydraulic systems and others. Varnish results from oil degradation in high-heat areas of equipment, creating clusters of deposits that adhere to metal surfaces, often deep within a piece of machinery. It can impair operational efficiency and, in the worst case, accelerate the end of equipment life.
In an earlier article, we detailed the causes and effects of varnish, and a successful varnish removal case study using Chevron’s VARTECH® ISC. Added to the oil just prior to a planned change, VARTECH ISC works by dissolving plated varnish into sub-micron particles in the oil, which are then expelled when the oil is completely flushed out.
We hear a lot of questions about varnish, cleaning solutions in general, and VARTECH ISC in particular. What follows are some of the most common.
How do I know I have a varnish problem?
Typical symptoms include sticky servo or thermostatic valves, sticking hydraulic cylinders, inefficient oil coolers leading to high oil temperatures, high bearing temperatures, and subsynchronous vibration (lower than normal frequency) in high-speed bearings and seals.
What tests will definitively prove I have varnish?
Tearing down the system to visually inspect for deposits is the only definitive way to determine the presence of varnish. Analysis of in-service oil can tell you only whether there is varnish or potential for varnish in the oil. It can suggest, but does not definitively confirm, whether performance issues are varnish-related.
Why should I clean varnish from my system?
Varnish affects both machine operation and the performance of newly installed oil. Removing varnish often restores a machine’s operating efficiency and prepares a system for better performance after an oil change.
How often should I use a cleaner?
Many operators choose to use a chemical cleaner as part of every oil change process. Others choose to clean only when operational evidence of varnish deposits are present. It should at least be considered every time you plan an oil change.
Can I use a cleaner as a top-treat life-extender to control varnish during operations?
Some commercially available cleaners claim they can be used indefinitely. However, Chevron does not endorse this approach. Chemicals in the cleaner can adversely alter the balance of the oil formulation, which may in turn impair lubricant performance. In addition, varnish and other contaminant particles remain in the system until the oil is drained. VARTECH ISC is designed as an end-of-oil-life cleaner precisely to avoid these issues.
Can I add VARTECH ISC to a lubricant to make it varnish resistant?
No. Chevron offers lubricants that are specially formulated with VARTECH technology to prevent varnish. However, VARTECH Industrial System Cleaner is designed to remove varnish and uses different chemistry.
How will the cleaner affect how I operate my system?
Most equipment can be used in normal operation while the cleaner is in the system. After the cleaner is added to the existing oil, operating parameters should be watched to identify evidence of cleaning success and indicators that filters need to be changed.
Will the cleaner plug the system’s filters?
Some cleaners have a propensity for plugging filters. VARTECH ISC dissolves varnish instead of flaking it off in chunks, which is what clogs filters. It’s been extensively tested in the field and, because of its dissolving properties, it has not plugged filters, even in equipment where other cleaners have done so repeatedly.
Will the cleaner remove all the varnish from my system?
The varnish chemistry will vary throughout the system. Soft varnish in coolers and sludge in reservoir bottoms often clean quickly and completely. Hard, polymerized deposits or those containing contaminants can be very stubborn and may remain after cleaning. Cleaning depends on lubricant flow to dissolve and remove the varnish from the area. Areas with low oil flow or low temperatures are unlikely to be completely cleaned, although a good cleaner will soften the varnish to ease manual removal.
Why should I drain effectively before refilling with fresh oil?
Old, degraded oil mixed into the refill oil will diminish the performance of the fresh oil. Residual cleaner may affect the performance and reduce the expected life of the fresh oil. VARTECH ISC is specifically formulated to be compatible with many circulating oils, including R&O, turbine and hydraulic oils, minimizing the impact of residual cleaner on the fresh oil.
Do I have to rinse flush after cleaning?
Rinse flushing is a best practice to completely remove old, degraded oil from all parts of the system. Complete draining of all the old oil and cleaner mixture helps mitigate the negative impacts on new oil performance. VARTECH ISC was formulated to be highly compatible with modern high-quality lubricants to minimize the risks of an incomplete drain or rinse.
Can I use the cleaner myself or do I need a service provider?
That depends on the complexity of your system and the capabilities of your team. Simply adding the cleaner, operating the system, and then performing a thorough oil change can be an effective approach. A service provider often brings valuable experience and can be very beneficial in confined space entry for reservoir wipe down, certified oil disposal, filter changes, and providing auxiliary heat for offline cleaning. They can also aid in determining cleaner residence durations and application concentrations.
How do I know if a cleaner has worked?
Although the evidence will vary among different systems, look for factors such as:
- Reduced temperature across oil coolers
- Lower bearing temperatures
- Reduced valve sticking or delayed actuation (hysteresis)
- Reduced vibration
- Visual observation of reduced deposits
- Darkening oil color during the cleaning, indicating that insoluble varnish precursors
remain stabilized in the oil - Captured debris in filters
How long will my system stay clean after I clean it?
That depends on whether the root cause of oil degradation has been addressed. Identifying and eliminating the root cause of oil degradation specific to your system will greatly improve oil life and system cleanliness. Your system will stay cleaner for longer if you refill with a high grade, varnish-resistant oil.
In what applications can I use VARTECH ISC?
VARTECH ISC has proven effective in many:
- Hydraulic systems
- Circulating systems
- Combustion turbines
- Steam turbines
- Flooded screw compressors
- Gear reduction systems and pumps using R&O or AW oil in lower viscosity grades
VARTECH ISC is intended for use in mineral and PAO synthetic oils, but not in exotic synthetic chemical lubricants such as PAG, POE, or diester fluids. It’s not ideal for reciprocating compressors, as their varnish often occurs in valves which don’t get much oil contact. In addition, the lower viscosity (55 cSt) of VARTECH ISC may lower the viscosity of a high-viscosity lubricant beyond OEM recommendations.
Still have questions about varnish? Just contact your Chevron Lubricants representative.
07/25/2024