Simple solutions for meeting equipment manufacturer’s oil cleanliness specifications Part 2: Monitor
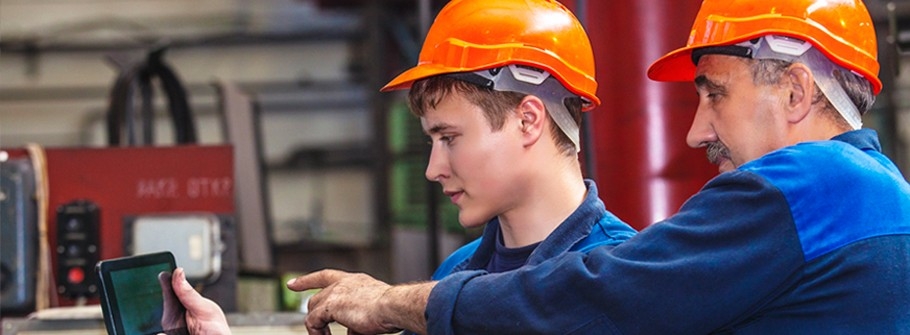
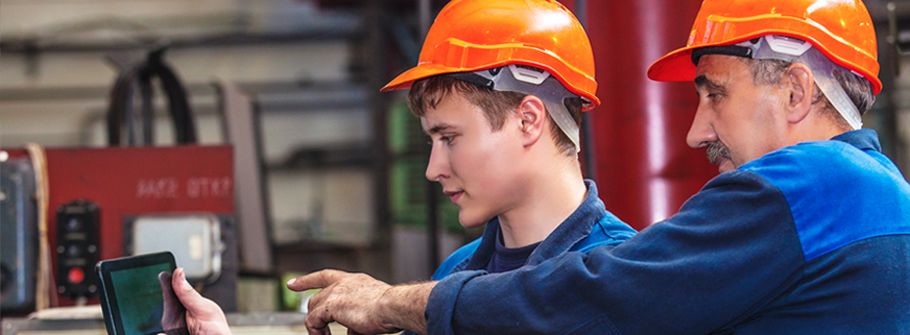
This is the second of a three-part series discussing the phases of an effective lubricant cleanliness program: Start Clean, Monitor and Stay Clean.
In our first article in this series, we set the stage for a lubricant cleanliness program by explaining how to “start clean.” The second phase of the program is monitoring lubricants for contamination while in service.
Regular intervals of oil analysis and condition monitoring are required to effectively understand and manage lubricant contamination levels as well as component wear and lubricant condition.
- For example, you should have oil analysis performed on critical in-service equipment at minimum once per month to measure particle counts against the baseline established in the “start clean” phase. The oil analysis should also look at all of the elements, including additives, metals, viscosity, and evidence of oxidation or moisture. Oil analysis should also be performed on new oil storage at minimum once per quarter to measure particle counts against the baseline established in the “start clean” phase.
- For equipment and applications where moisture can be a critical issue, you will want to test specifically for the presence of water contamination. The Karl Fischer Titration Method, named for the German chemist who invented it, is a widely accepted standard for determining trace amounts of water in a sample.
- If your operation includes the potential for varnish formation or maintains high temperatures, you should be constantly monitoring and trending varnish. The Membrane Patch Colorimetry or MPC test, performed quarterly on in-service equipment is a good test to include with your oil analysis program.
For all of these elements of oil analysis, you will need to set limits for acceptable levels. Once these limits have been exceeded, it is critical to set up corrective action plans. Work with your lubricant supplier to set up these corrective action plans at the very beginning so the processes and procedures are in-place and ready to be implemented to minimize any potential downtime due to failure. For example, if particle contamination exceeds the set limit, your lubricant supplier can have a kidney loop filter ready for installation and begin cleaning the in-service oil while the equipment continues operation.
The key to any oil analysis and condition monitoring program is consistency on properly pulling of samples as well as trending of the data. Making corrective action decisions on single data points is not a good practice. Trending the data and making decisions on these trends is very important. Review data on a regular basis and include your lubricant supplier.
Remember it is important to perform the sampling correctly and to have the correct tests performed for your specific application. If you have questions, your lubricant supplier should be able to provide guidance on the proper sampling and testing procedures. If you struggle to find time and resources to set up and manage this type of program, work with your lubricant supplier to provide or assist in sourcing this type of service. Chevron’s new ISOCLEAN® Program is a simple solution to get you started.
Once you have a regular monitoring program in place, there are specific steps you can take to make sure you “stay clean” based on your testing results and trending data. We’ll explore those in a future article.
01/19/2017