Are you optimizing your fleet? Or compromising it?
Many fleets are buying name-brand lubricants that are not necessarily tailored to their specific applications
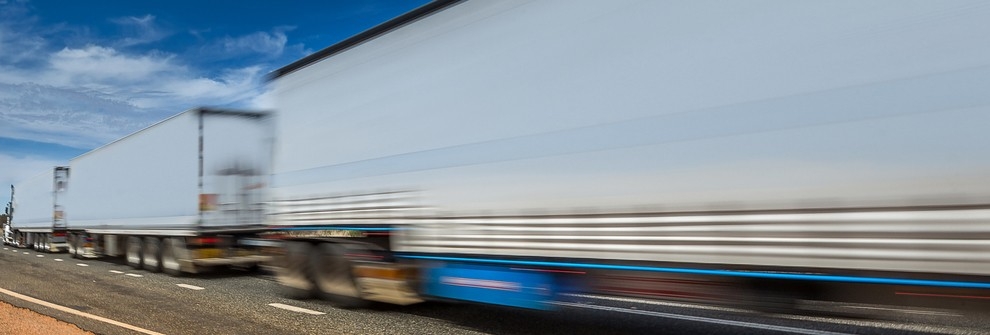
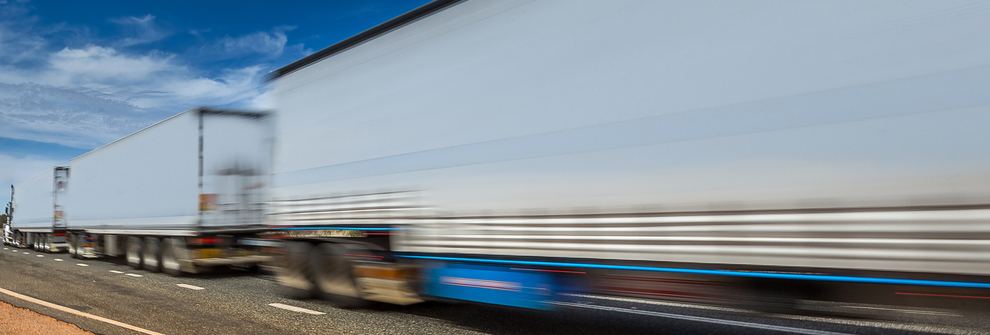
A former customer of ours in Canada recently lost its independence to a competitor. Faced with tightening budgets, they began making decisions solely on price, including using cheaper oils and following generic maintenance protocols across their fleet. Instead of saving them money, this approach had exactly the opposite effect – unplanned equipment downtime and increased maintenance costs. Eventually it snowballed into unreliable operations and a loss of customers. Ultimately it became an unprofitable business, with no choice but to sell out. The new owners cherry-picked the fleet’s assets and employees and liquidated the remaining resources.
Their story is an object lesson for fleet operators on both sides of the border. We see many fleet managers buying name-brand lubricants that are not necessarily tailored to their specific applications, operating conditions, or maintenance objectives, which vary from fleet to fleet. This approach results in fleet managers not optimizing drain intervals, fuel efficiency and downtime. And losing money as a consequence.
Let’s take a look at a different company that undertook an assessment of its lubrication practices. The company’s fleet was comprised of 1,000 Class 8 trucks and they were completing drain intervals at 35,000 miles/56327 km. They averaged two to three oil changes and new filter kits per vehicle per year, and each truck consumed 11 gallons of engine oil on average at around $7.50 per 3.785 liters. A day of downtime for maintenance cost them $2,000 in revenue per truck.
What did this all mean in dollars? By using a lower quality lubricant and not optimizing drain intervals, they were performing one unnecessary oil change each year that cost them about $90,000 in oil and filters. They were also losing one day of revenue per truck per year due to maintenance downtime, or $2 million per year for the fleet. And by using an oil that didn’t deliver fuel efficiencies, they were wasting $643 per year per truck, or $643,000 in fuel alone – around 1.7% of total annual fuel costs.
Put in a more positive light, this assessment uncovered potential expense reductions of around $2.7 million per year by optimizing drain intervals, fuel efficiency and downtime.
Without question, it’s a challenge to keep up with the latest trends, such as the transition to lower viscosity oils, EPA greenhouse gas (GHG) regulations, new OEM specs and drain optimization. However, many fleet managers have saved millions of dollars by assessing and defining the specific applications of their fleet and using the optimal lubricant to help extend maintenance intervals. This, in turn, improves on business objectives such as service uptime, average miles per truck, tonnage per mile, and longer equipment life.
With expert advice on new technology, combined with testing protocols, you’ll be able to identify the right products to deliver optimized drain intervals, fuel efficiency, and downtime. And you’ll enjoy the peace of mind knowing that you are running your fleet consistently with OEM recommendations while maximizing your fleet’s performance.
12/12/2017